How Is Paper Made Today?
Paper products are an essential part of daily life. Our mills operate year-round to manufacture and ship products such as cardboard boxes, packaging, pulp for diapers, toilet paper and paper for mail.
U.S. pulp, paper, tissue and packaging manufacturers rely on a complex supply chain to produce these goods. The economic impact of these manufacturing activities and our supply chain is significant.
Paper’s Raw Materials
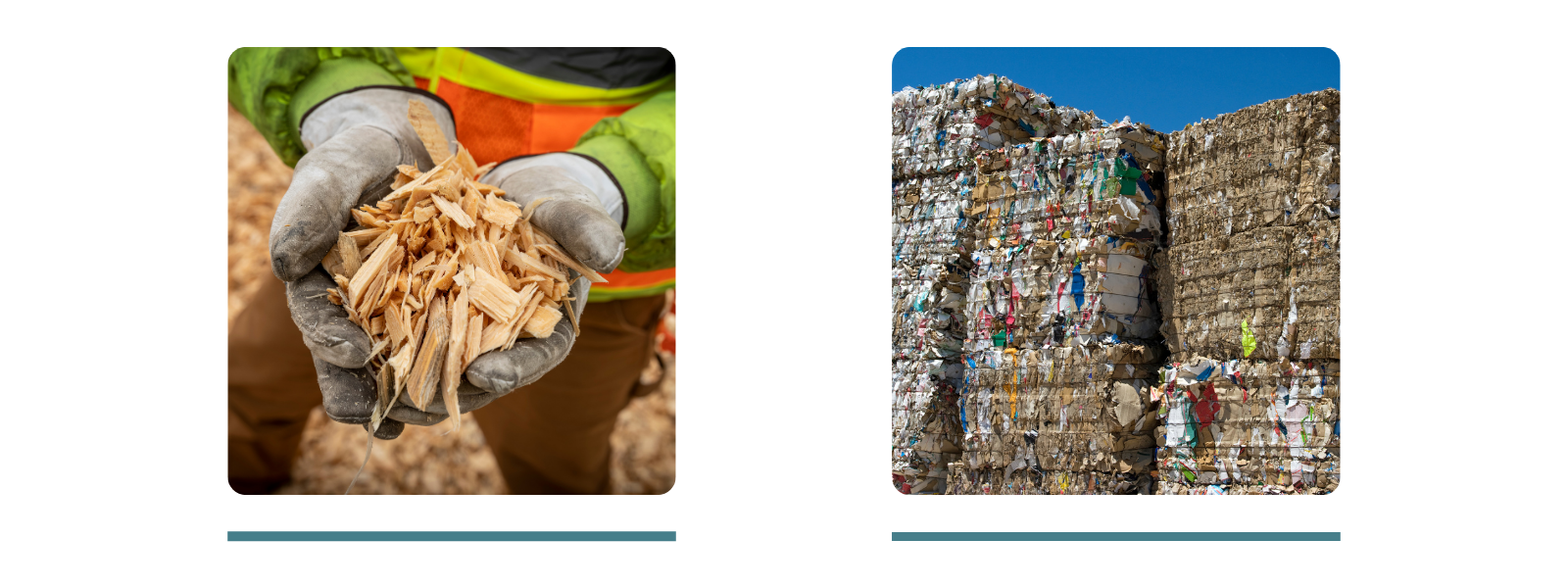
To make paper products, manufacturers must first source their raw materials. Our industry relies on 2 primary feedstocks:
Wood that is unsuitable for building materials, which creates fresh wood pulp. This can include:
- Branches
- Tree tops
- Stumps
- Bark
- Wood leftovers from sawmills, like sawmill dust and chips
- Trees from forest thinnings, a necessary process to keep forests healthy
- Pulpwood, which are small trees that can’t be turned into lumber
Recycled paper and paper-based packaging. This creates recycled paper pulp.
The type or amount of raw material manufacturers use depends on the different characteristics of the product they’re trying to achieve.
Sourcing Materials for Fresh Wood Pulp
Our industry sources materials from:
- Managed working forests. In fact, 90% of our wood materials comes from nearly 11 million small, private, non-commercial family forest owners. We source branches, treetops, pulpwood and more from these private working forests.
- Sawmills. We source materials like chips and sawdust.
Our industry uses materials that cannot be turned into lumber and transforms them into essential, everyday products.
Pulping: Breaking Down the Fibers
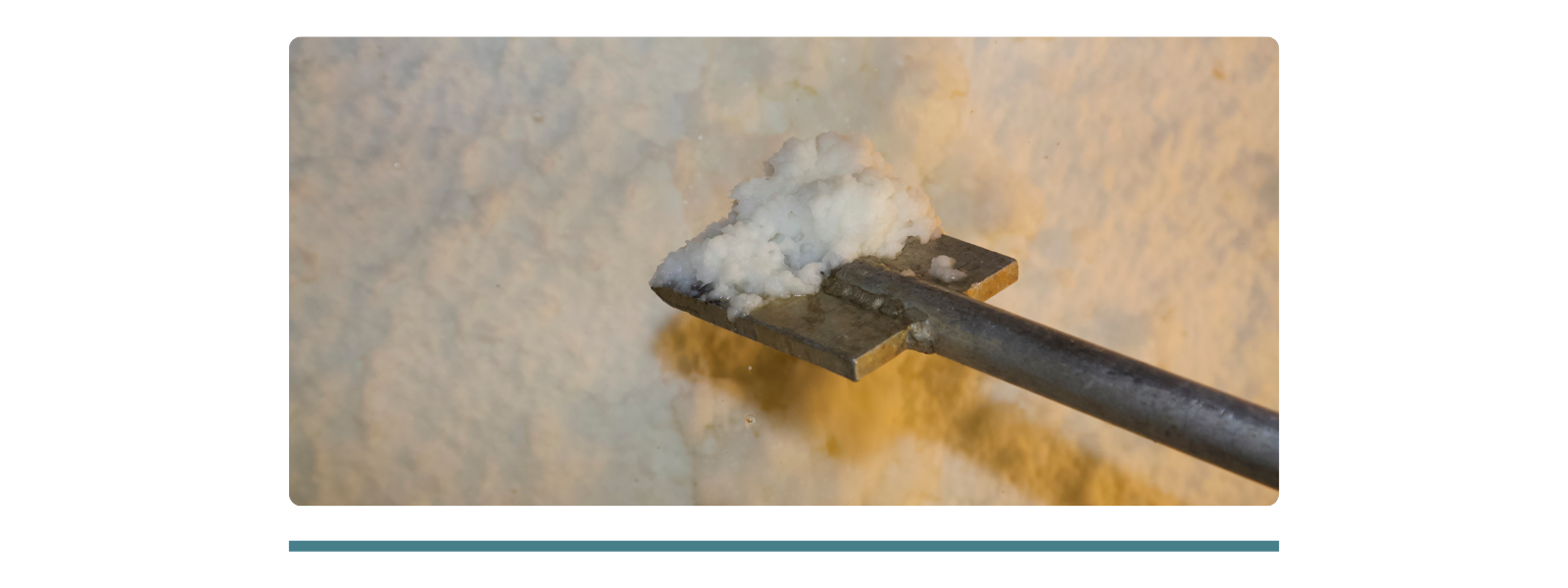
The first step in the papermaking process is pulping.
During the pulping process, the natural glue – lignin – is broken down and dissolved leaving manufacturers with cellulose. Cellulose is the structural backbone of paper products.
The type of pulping process manufacturers use depends on the raw materials and what’s being produced.
- Mechanical pulping: Physically grinds wood, which helps keep the lignin in the pulp. Keeping lignin in the pulp means more pulp is produced. It’s used for things like newspapers, tissue products and paperboard.
- Chemical pulping: Uses heat and a variety of chemicals to remove the lignin. Using chemicals allows the cellulose fibers to separate without losing their strength or length. This pulp creates paper products best used for printing.
- Repulping recycled paper: Paper and packaging that is collected from residential, commercial, industrial and institutional recycling streams are mixed in a giant blender called a repulper.
From Pulp to Finished Products
Forming, Pressing, and Drying
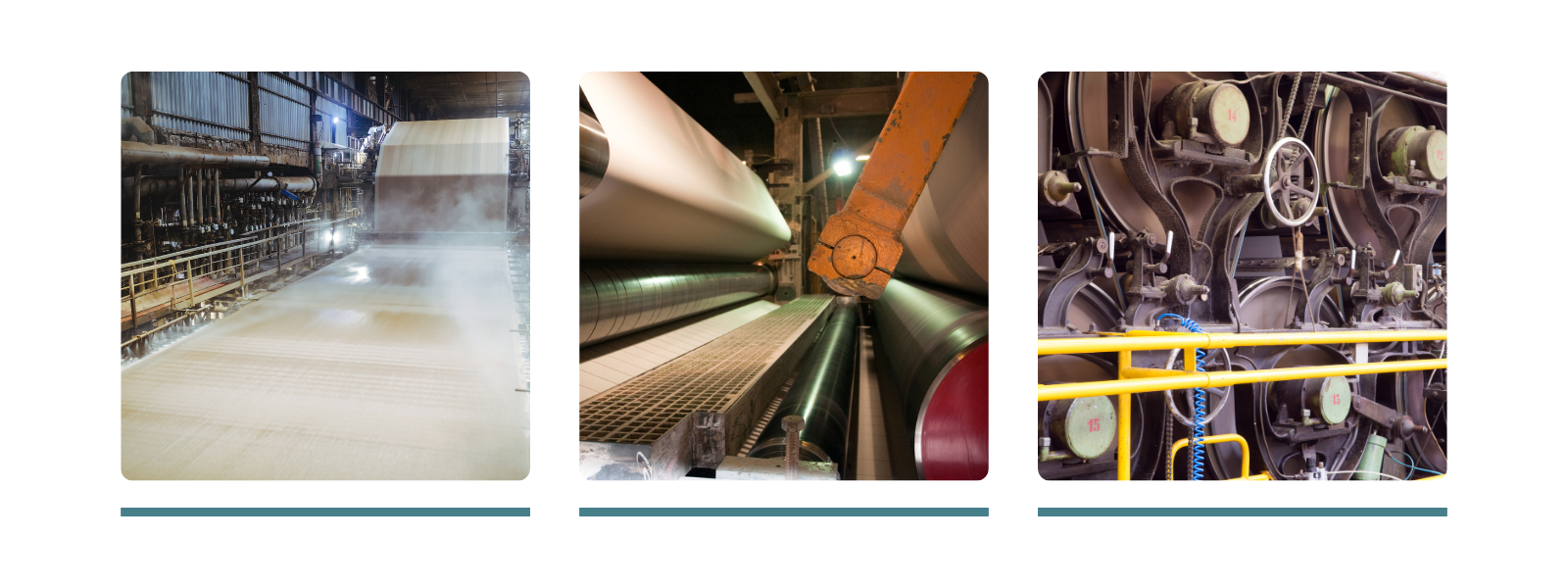
The pulp is mixed with water and spread onto a screen, letting the water drain. Then, rollers press out more moisture, and heated cylinders dry the sheet until it contains about 5% water.
Winding and Transport
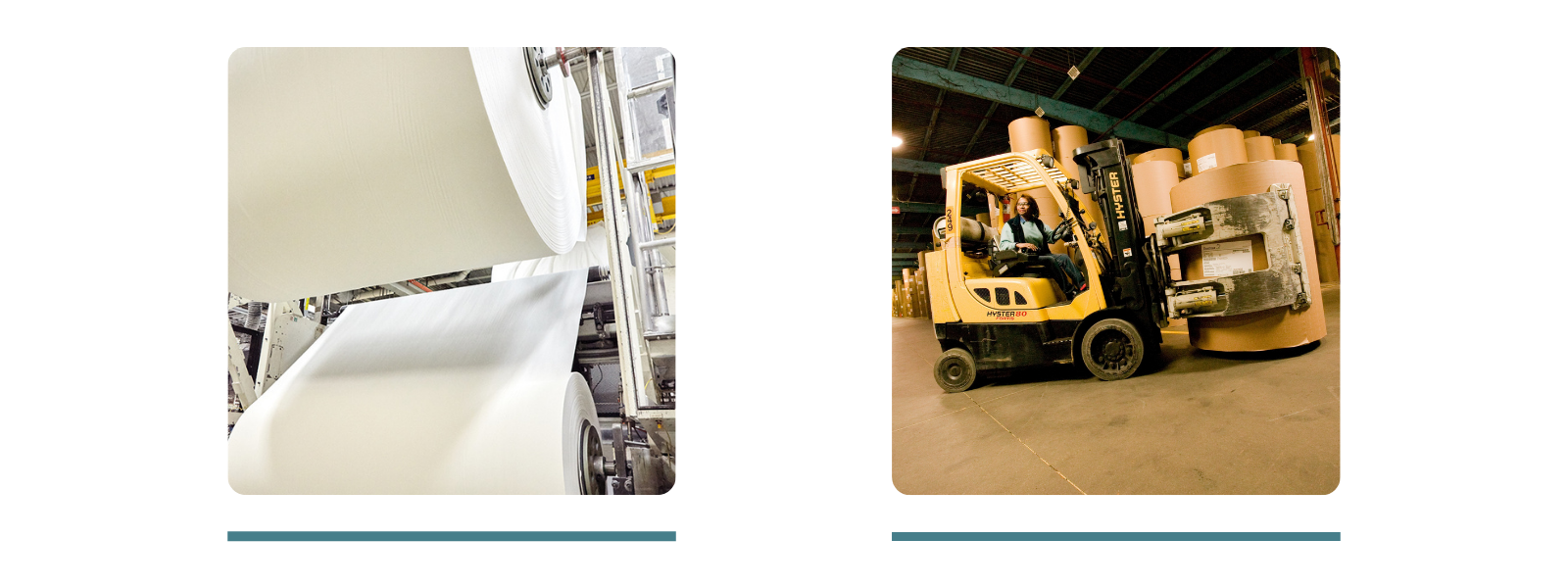
The dried paper is smoothed and wound into large rolls. These are called parent rolls. The parent rolls are then sent to converting facilities.
Finished Paper Products on Store Shelves
The paper products are then sent to distributors and wholesalers who then sell the products to retailers. Once the finished paper product arrives at a retailer, it’s placed on the store shelf for purchase.
Photo Credits: Domtar and Procter & Gamble
EXPLORE
The U.S. forest products supply chain is complex and highly integrated with Canada and Mexico.
Explore paper's complex manufacturing journey and discover how North American tariffs affect the industry.
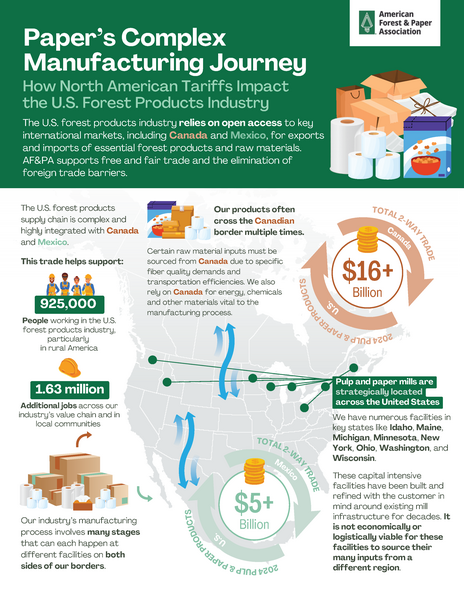